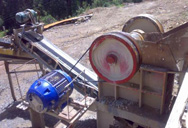
Operational parameters affecting the vertical roller mill
2017年4月1日 Vertical roller mills (VRM) have found applications mostly in cement grinding operations where they were used in raw meal and finish grinding stages and in power
learn more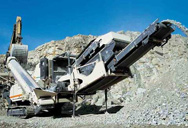
Review on vertical roller mill in cement industry its
2021年1月1日 With proper optimization of these parameters, the productivity of vertical roller mill can be improved and performance stability can be achieved by addressing root
learn more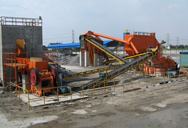
Numerical Investigation of Vertical Roller Mill Operation
2023年12月4日 A vertical roller mill (VRM) is a grinding equipment used for the size reduction of minerals, cement, and ceramics. The capacity of the VRM depends not only
learn more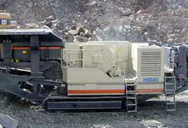
Review on vertical roller mill in cement industry its
2021年1月1日 The cement mill is either a Ball mill with two chambers or Vertical roller mill with inbuilt classifier. Material is ground till desired Blaine is achieved and then final
learn more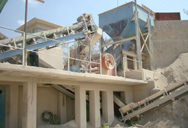
Full article: Reliability assessment of the vertical roller mill
The vertical roller mill (VRM) is heavy mechanical equipment that used in the cement materials industry to process cement, slag, and coal cinder (Pani Mohanta, Citation
learn more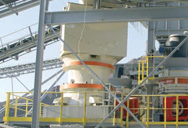
Expert PID Control of Grinding Condition for Cement Vertical Roller Mill
This paper proposed a controller design method based on expert PID to automatically control the load and quality of cement vertical mill. This method is applied to a cement
learn more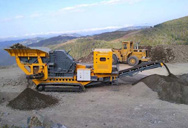
The Cement Plant Operations Handbook - International
2019年4月30日 Clinker – 11. Finish mill – 12. Cement – 13. Quality control – 14. Packing and distribution – 15. Emission abatement (dust, NO x, SO 2, etc) – 16. Maintenance –
learn more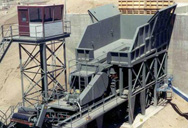
Grinding Process Optimization - Featuring Case Studies
2023年12月6日 The modular vertical roller mill for grinding cement raw material, cement clinker, and additives with an installed power of up to 12,000 kW was specifically
learn more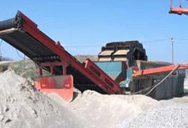
OK™ Raw and Cement Mill - FLSmidth
Our best-in-class OK™ Mill is a globally successful vertical roller mill solution for grinding raw material, cement and slag. Its cutting-edge design features consistently deliver the
learn more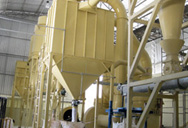
Vertical roller mills FLSmidth Cement
OK™ Raw and Cement Mill. Our best-in-class OK™ Mill is a globally successful vertical roller mill solution for grinding raw material, cement and slag. Its cutting-edge design features consistently deliver the highest quality products with the greatest efficiency. It is affordable to install and cost effective to operate over your cement ...
learn more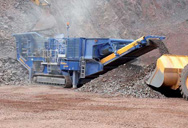
Vertical Cement Mill Magotteaux
Magotteaux’s advanced vertical cement mill technology ensures consistent results by providing precise control over the grinding process, enabling the production of high-quality cement with minimal variations in fineness. Our adjustable speed drives and advanced process control systems allow operators to accurately monitor and adjust grinding ...
learn more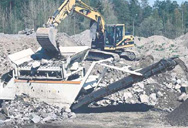
Numerical Investigation of Vertical Roller Mill Operation
2023年12月4日 A vertical roller mill is a grinding equipment for many industries such as minerals, cement, and ceramics. It is also used to grind slag and nonmetallic ores. The VRM decreases the number of equipment in the grinding circuit by combining the drying, crushing, grinding, and particle segregation in one unit [ 1 ].
learn more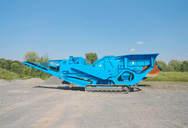
GitHub
opération de google cement mill. Grinding in Ball Mills: Modeling and Process Control. minerals,limestone,etc.The applications of ball mills are ubiquitous in mineral processing
learn more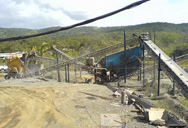
(PDF) CEMENT RAW MATERIAL GRINDING ; VERTICAL ROLLER MILL OPERATION ...
Enter the email address you signed up with and we'll email you a reset link.
learn more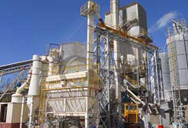
fr/ciment opération mill.md at main hongyib/fr
Contribute to hongyib/fr development by creating an account on GitHub.
learn more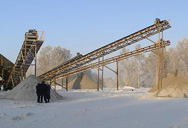
Unstable vibration of roller mills - ScienceDirect
2006年10月24日 Over the past 30 years, roller mills have been rapidly employed and widely used to process raw materials in the cement industries because of their superior high efficiency [1], [2], [3]. Recently, roller mills have come to be adapted to the grinding of other materials such as ceramic, filler material, etc. due to their power saving capability [4].
learn more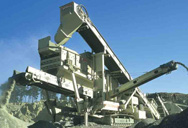
PROCESS TRAINING for operators of Vertical RAW Mills
During heat up there should be a sufficient air flow through the mill to force the heat transfer to the grinding part – forced convection. A sufficient air flow will result in a mill differential pressure of> 5mbar. The duration of heating should be at least until the temperatures after mill and after bag filter reach 85° C.
learn more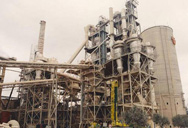
Coal mill, gypsum mill, clay mill, etc. Pfeiffer MPS mills
MPS 3070 BK coal mill, Jaypee Cement Balaji, India. MPS 180 GC vertical roller mill for the grinding, drying and calcining of gypsum, Knauf Knin, Croatia. MPS 100 GC vertical roller mill for the grinding, drying and calcining of gypsum, Trevo, Brasil. MPS 3350 B mill for limestone grinding, China Chongqing Foreign Trade Huaneng, China.
learn more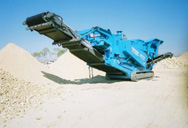
DESIGN AND ANALYSIS OF BALL MILL INLET CHUTE FOR
2019年4月21日 The dimensions/areas for a chute should as far as possible be chosen according to. the outlet flange for a machine. The smallest side length in a chute must be min. 5 times the max lump size. Min. chute size for lumpy material: 250mm x 250mm (0,063 m2). Min. chute size for powdery material: ø200 (0.04 m2).
learn more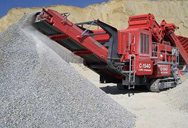
How it Works Roller Mill
2023年9月15日 A rolling mill is a mill that uses compression on a single, double or even triple cylindrical wheel that is rotated along the long axis against another wheel or a plate. The cylindrical wheels are mounted horizontally and only one is run by a motor to move the grains between the two wheels while the other moves slowly as a result of friction ...
learn more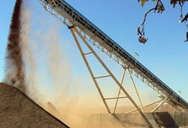
Raw mills for all requirements Gebr. Pfeiffer
The cement raw material mixtures are ground, dried, and classified in the Pfeiffer vertical roller mill. For drying the material, hot gases are directed into the mill. Product fineness can be adjusted within a wide range (0.063 to
learn more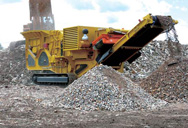
Cement Roller Press - Roller Press In Cement Plant
When grinding cement, the abrasion of the ball mill is 300-1000 g/t, while that of the roller press is 0.5g/t, so it can meet the requirements of grinding white cement. Low Noise The noise of the ball mill is more than 110d,
learn more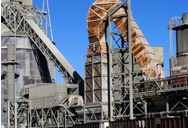
Horizontal roller mill (Horomill®) application versus hybrid HPGR/ball ...
2009年12月1日 1.. IntroductionConventionally multi-compartment ball mills are used in finish grinding of cement. However, they are relatively inefficient at size reduction and have high energy consumption, so it is increasingly common to find grinding technologies such as High Pressure Grinding Rolls (HPGR), vertical mills and Horomill ® in cement plants. As
learn more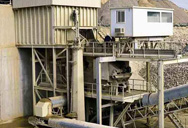
Cement Industry Loesche
2024年5月7日 Cement Industry. LOESCHE Vertical Roller Mill: We do much more than rely solely on our unbeatable technology. Our designers are constantly coming up with new ideas and even more dependable components to reduce the already acclaimed low failure rate of our mills. The roller grinding mill technology, patented in 1928 and continuously
learn more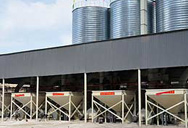
Operational experience from the United States' first vertical roller ...
For several decades the cement industry has successfully utilized vertical roller mills (VRM) for grinding of raw materials and solid fuels. Most recently, this technology has been employed for the combination of Portland cement, blended cements and slag cements. The VRM offers several benefits compared to the ball mill in regards to operating costs and
learn more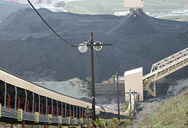
Full article: Reliability assessment of the vertical roller mill
1. Introduction. The vertical roller mill (VRM) is heavy mechanical equipment that used in the cement materials industry to process cement, slag, and coal cinder (Pani Mohanta, Citation 2015).The equipment always needs to work in the environment of heavy load, high temperature, high pressure, high corrosiveness, electromagnetic radiation interference,
learn more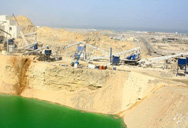
Cement Grinding - Cement Plant Optimization
Vertical Roller Mills (VRM). Roller press with Ball mill. Ball Mill. Ball mills with high efficiency separators have been used for cement grinding in cement plants all these years. Ball mill is a cylinder rotating at about 70-80% of critical speed on two trunnions in white metal bearings or slide shoe bearings for large capacity mills.
learn more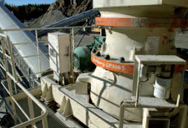
Cement grinding Vertical roller mills VS ball mills
For a ball mill grinding OPC to a fineness of 3200 to 3600 cm2/g (Blaine) the cost of wear parts (ball, liners and mill internals) is typically 0.15-0.20 EUR per ton of cement. For an OK mill grinding a similar product, the cost of wear parts depends on the maintenance procedures, i.e. whether hardfacing is applied.
learn more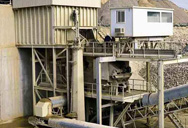
Mineral Processing Machine Operators Gouvernement du
DVS in opération d'équipements de production . Code : 5362. Placement rate: 80.4%. ... Roller plate mill - primary metal processing Temper mill roller - primary metal processing ... Concrete batch plant operator - cement manufacturing Charging machine operator - mineral and metal processing ...
learn more