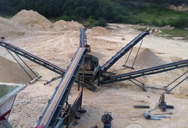
Grinding in Ball Mills: Modeling and Process Control
• characteristics of the grinding media (mass, density, ball size distribution); • speed of rotation of the mill; • slurry density in case of wet grinding operation. Quantitative
learn more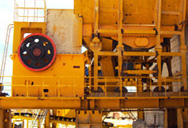
(PDF) Effect of Slurry Density on Load Dynamic
2012年4月17日 In ball milling, the transmission of grinding energy from the steel balls to the particles in the slurry is closely linked to the way the
learn more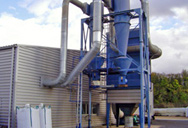
Slurry density effects on ball milling in a laboratory ball mill
Slurry density effects on ball milling in a laboratory ball mill Semantic Scholar. DOI: 10.1016/0032-5910 (89)80087-7. Corpus ID: 95911523. Slurry density effects on ball
learn more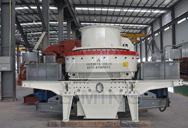
Ball Mill - On-line Estimation of In-mill Slurry Density.
2023年9月1日 The slurry density was set to different values by adapting the water addition flow at the mill inlet. The mill is equipped with a Sensomag which provides information
learn more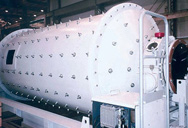
Effect of Slurry Density on Load Dynamic and Milling
PDF. In ball milling, the transmission of grinding energ y from the steel balls to the particles in the slurry is closely linked to the way the media a nd the slurry are mixed. One of the
learn more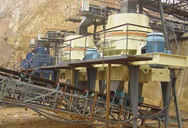
Effects of filling degree and viscosity of slurry on mill load ...
2011年10月1日 Ball filling and mill fractional speed were kept constant respectively at 20% and 60% while slurry filling was varied from 0% to 300%. Using a high speed video
learn more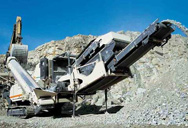
Optimization of Solids Concentration in Iron Ore Ball
2019年6月18日 Keywords: iron ore; ball mill; modeling; simulation; population balance model; slurry density 1. Introduction It has been well over half a century since Austin and
learn more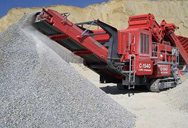
Optimization of Solids Concentration in Iron Ore
2019年6月18日 Important advances have been made in the last 60 years or so in the modeling of ball mills using mathematical formulas and models. One approach that has gained popularity is the population balance
learn more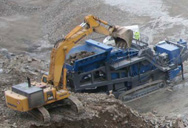
Multivariate approach to on-line prediction of in-mill slurry density ...
2012年1月1日 Graphical abstract. The slurry density and ball load volume inside a laboratory ball mill have been estimated by two statistical multivariate methods: (i) partial least squares – PLS and (ii) combination of PLS and radial basis functions neural networks (RBF-PLS) based on characteristic features contained in the ball and slurry sensor data.
learn more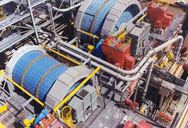
Slurry Densities - The Engineering ToolBox
2024年5月8日 Slurry Densities. Slurry is a mixture of a solid and a liquid. The density of a slurry can be calculated as. ρm = 100 / [cw / ρs + [100 - cw] / ρl] (1) where. ρm = density of slurry (lb/ft3, kg/m3) cw = concentration
learn more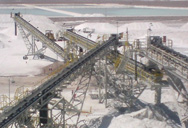
Slurry density effects on ball milling in a laboratory ball mill
Semantic Scholar extracted view of "Slurry density effects on ball milling in a laboratory ball mill" by C. Tangsathitkulchai et al. Skip to search form Skip to main content Skip to account menu. Semantic Scholar's Logo. 217,028,989 papers from
learn more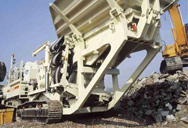
Ceramics: Effect of Powder and Slurry Properties on Quality
2013年10月17日 The powder was placed in alumina ball mill container (SSA-999, Nikkato, Japan, volume 2000 ml) with 2 kg of alumina balls (SSA-999, Nikkato; diameter 5 mm), and 400 g of aqueous solution (2 % w/w) of dispersant of polyacrylic acid type (CERUNA D-305, Chukyo Yushi, Japan) and mixed for 24 h to make a slurry with 50 % v/v solid content.
learn more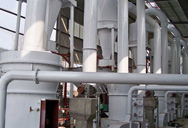
Power predictions for a pilot scale stirred ball mill
1996年3月1日 The slurry density also had a strong influence on the power draft. Thus changing the slurry density by only 10% from 65% to 75% caused the mill power draft to increase from 4 kW to 6 kW. From the correlation alone, the slurry density had a stronger effect than the mill speed. It had a power of 2.95 as is seen in Fig. lb.
learn more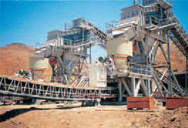
Effect of Slurry Solids Concentration and Ball Loading on Mill ...
2014年3月2日 3.1. Industrial Ball Mill The ball mill utilized in the sampling survey has an inside diameter of 7.3 m and length of 9.6 m and is run in open circuit. Under normal operating conditions, the mill ball loading is 30% of total mill volume, mill rotational speed is 75% of critical speed, slurry solids concentration is 75%, solids feed rate is 330 tph.
learn more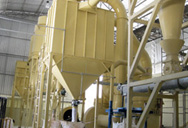
Measuring Density in Grinding Circuit - Rhosonics
As an example, a recommended application to efficiently dose grinding media (balls) and water into the ball mill is measuring density changes in the ball mill discharge. Why control over parameters is important. In this paragraph, we will explain why control over parameters, such as the particle size and slurry density, is important to reach an ...
learn more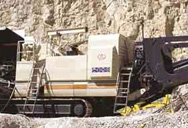
Slurry Density Calculator - Savvy Calculator
A Slurry Density Calculator is a practical tool used in various industries, including mining, metallurgy, and wastewater treatment, to determine the density of a slurry mixture. A slurry is a semi-liquid mixture composed of solid particles suspended in a liquid, such as water. The density of a slurry is essential for optimizing processes and ...
learn more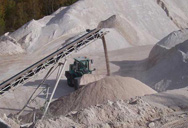
A study on the effect of parameters in stirred ball milling
1993年1月1日 INTRODUCTION The parameters of the Drais stirred ball mill such as the feed size, bead size, flow rate and bead load have been studied by Gao and Forssberg ( 1992 ). In this work, another four parameters of this mill will be examined. They are the bead density, slurry density, mill speed, and the effect of dispersant.
learn more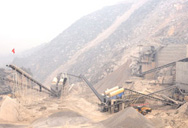
Effects of slurry filling and mill speed on the net power draw
2014年2月1日 In the case of wet milling, slurry is identified by a signature that comes with the fluid carrier in the form of electrical conductivity. Fig. 4 shows the set-up of a conductivity sensor in which a bolt is used as the sensing element. The bolt plays the role of the live electrode while the mill shell is the electric ground. ... Ball density, ρ ...
learn more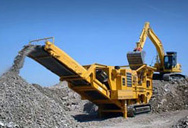
Slurry mill BMA's supply line of crystallization
Slurry mill. Especially for seeding as a preliminary stage of product crystallization proper, the use of a slurry suspension is now state of the art. BMA's supply line of crystallization equipment also includes a slurry mill
learn more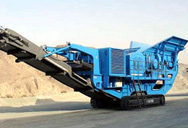
Should the slurry density in a grinding mill be adjusted as a
2007年7月1日 The slurry density or pulp percentage of solids and the size of the grinding media are often considered for ball mill optimization. Laboratory grinding tests were conducted to identify possible ...
learn more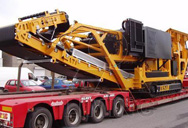
Wet jet milling of Al2O3 slurries - ScienceDirect
2007年1月1日 A wet-rotating disc milling was used as a method to prepare ceramic slurry. The rheological measurements of the milled slurries showed that the apparent viscosity of the wet-rotating disc milled slurry was low and the slurry was nearly Newtonian behavior, whereas that of ball-milled slurry was more viscous and the slurry exhibited a very strong
learn more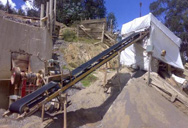
Mixing methods for solid state electrodes: Techniques,
2023年5月15日 Excellent reviews have been published summarizing the state-of-the-art in wet-based [10] or dry [11] slurry preparation, production engineering and production scenarios for the fabrication of -SSBs [12], slurry characterization, coating and drying [13], fundamentals of planetary ball milling for SSB, [14] and the processing techniques
learn more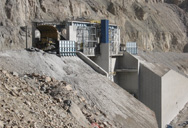
Characterization and performance analysis of silicon carbide ...
2002年4月20日 The pH of the SiC powder dispersed in de-ionized water is about 6.5. Addition of 13 wt.% PTFE increased the pH of the slurry to about 7.4.The results of the zeta potential measurements at various pH values of the slurries prepared by ball milling and mechanical stirring are shown in Fig. 2.The experimentally observed iso-electric point
learn more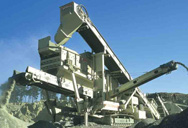
(PDF) DESIGN AND FABRICATION OF MINI BALL MILL
2016年3月25日 [22] Effect of Slurry Density on Load Dynamic and Milling Performances in an Iron Ore Ball Mill - On-line Estimation of In-mill Slurry Density Bernard de Haas, Alfred V an den Bosch, Axel Köttgen
learn more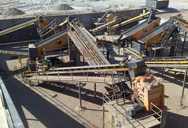
On the analysis of fine wet grinding in a batch ball mill
1996年9月1日 The influence of the slurry density on the fine wet grinding performances of a batch ball mill was examined for an alumina hydrate feed. Irrespective of the operating conditions, the size reduction process proceeds fast in the first period of grinding (20 min); then its rate progressively reduces and after 1–2 h the size of the product approches a
learn more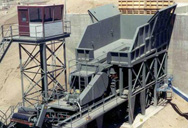
High Energy Density LiFePO4/C Cathode Material
of 0.51: 1: 0.09 to form a homogeneous slurry using a planetary ball miller(P5,Yunfan, Tianjin)at300rpmfor4h.Thezirconiaballwith a diameter of 1 mm was used for ball milling and the ratio of ball to material was 5: 1. Then the precursor slurry with a solid content of 35 wt% was spray-dried in a pressure spray dryer (LG–5, Jianyi,
learn more